Supplier Evaluation and Selection: Best Practices and Strategies
Supplier Evaluation and Selection: Best Practices and Strategies
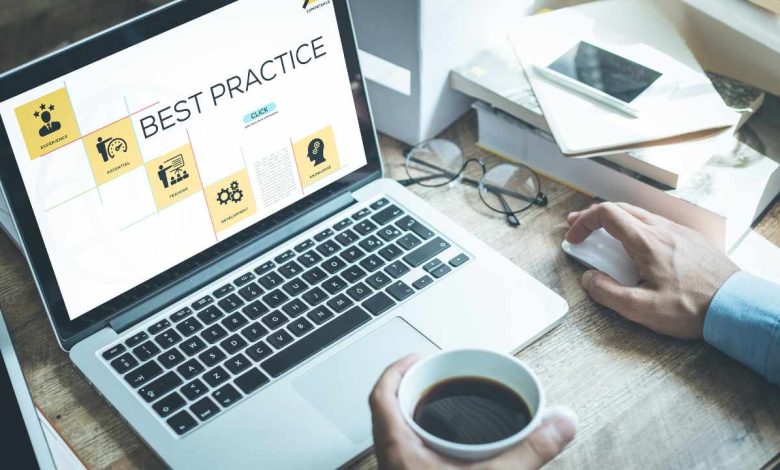
Supplier evaluation and selection are crucial processes for businesses aiming to maintain efficiency, quality, and competitiveness in their operations. In this article, we’ll delve into the key criteria, methods, best practices, and strategies for effective supplier evaluation and selection, along with the challenges involved and future trends in the field.
Introduction to Supplier Evaluation and Selection
Lieferantenbewertung und -auswahl. In today’s globalized marketplace, businesses rely heavily on suppliers to provide the goods and services necessary for their operations. Therefore, choosing the right suppliers is paramount to ensuring smooth and uninterrupted production processes. Supplier evaluation and selection involve assessing potential suppliers based on various criteria to determine their suitability for partnership.
Key Criteria for Supplier Evaluation
Quality
Quality is perhaps the most critical factor in supplier evaluation. It encompasses the reliability, consistency, and performance of the products or services offered.
Reliability
Reliability refers to a supplier’s ability to deliver goods or services consistently and on time. A reliable supplier helps businesses maintain their production schedules and meet customer demands.
Cost
Cost considerations are essential in supplier selection. While businesses aim to minimize costs, they must also ensure that the chosen supplier offers value for money without compromising on quality.
Responsiveness
A responsive supplier is proactive in addressing issues and concerns promptly. Effective communication and quick problem-solving are essential attributes of a responsive supplier.
Flexibility
In today’s dynamic business environment, flexibility is crucial. Suppliers capable of adapting to changing requirements and accommodating customization requests are highly valued.
Methods of Supplier Evaluation
Several methods can be employed to evaluate potential suppliers, including the use of supplier scorecards, on-site audits, and references from other clients.
Supplier Scorecards
Supplier scorecards are tools used to assess suppliers based on predefined metrics such as quality, delivery performance, and cost-effectiveness.
On-site Audits
On-site audits involve visiting the supplier’s facilities to evaluate their capabilities, processes, and adherence to quality standards.
References and Referrals
References and referrals from other clients provide valuable insights into a supplier’s reputation, reliability, and performance.
Best Practices in Supplier Selection
Conducting Thorough Research
Before selecting a supplier, it’s essential to conduct thorough research to gather information about potential candidates and their offerings.
Establishing Clear Criteria
Establishing clear criteria helps streamline the supplier selection process and ensures that all stakeholders are aligned on their expectations.
Involving Stakeholders
Involving stakeholders from various departments, such as procurement, operations, and quality assurance, ensures that diverse perspectives are considered during supplier selection.
Negotiating Terms
Negotiating favorable terms with selected suppliers is crucial for achieving mutually beneficial agreements that meet the needs of both parties.
Strategies for Effective Supplier Management
Effective supplier management involves more than just selecting the right suppliers—it requires ongoing efforts to build strong relationships, monitor performance, and drive continuous improvement.
Building Strong Relationships
Building strong relationships with suppliers fosters collaboration, trust, and transparency, leading to better outcomes for both parties.
Monitoring Performance
Regularly monitoring supplier performance enables businesses to identify areas for improvement and address issues promptly to prevent disruptions.
Continuous Improvement Initiatives
Implementing continuous improvement initiatives helps suppliers enhance their processes, capabilities, and offerings over time.
Technology and Tools for Supplier Evaluation
Advancements in technology have revolutionized supplier evaluation and selection processes, with tools such as supplier relationship management (SRM) software, data analytics, and automation playing crucial roles.
Supplier Relationship Management (SRM) Software
SRM software helps businesses streamline supplier management tasks, such as performance tracking, contract management, and communication.
Data Analytics
Data analytics enables businesses to derive valuable insights from supplier-related data, such as performance metrics, market trends, and risk factors.
Automation
Automation of repetitive tasks, such as invoice processing and order management, improves efficiency and reduces the administrative burden associated with supplier management.
Challenges in Supplier Evaluation and Selection
Despite the benefits, supplier evaluation and selection pose several challenges for businesses, including limited resources, changing market conditions, and the need for effective supplier risk management.
Limited Resources
Limited resources, such as time and budget constraints, can impede businesses’ ability to conduct thorough supplier evaluations and make informed decisions.
Changing Market Conditions
Fluctuations in market conditions, such as supply chain disruptions or economic instability, can impact supplier performance and availability.
Supplier Risk Management
Managing supplier-related risks, such as quality issues, delivery delays, and geopolitical instability, requires proactive risk mitigation strategies.
Case Studies: Successful Supplier Evaluation and Selection
Examining real-world examples of companies implementing effective supplier evaluation and selection strategies provides valuable insights into best practices and lessons learned.
Future Trends in Supplier Evaluation and Selection
Looking ahead, several trends are expected to shape the future of supplier evaluation and selection, including the integration of AI and machine learning, as well as increased focus on sustainability considerations.
Conclusion
Supplier evaluation and selection are critical processes that require careful consideration and strategic planning to ensure the success and sustainability of businesses. By adhering to best practices, leveraging technology, and addressing challenges proactively, businesses can forge strong partnerships with suppliers and drive continuous improvement in their operations.